Gelatin Processing Plants
Model : Gel-mix
Propack Technologies’ gelatin processing systems for batch sizes ranging from 10 L to 5,000 L are suitable to manufacture different types of Gelatin compounds like soft gelatin, hard gelatin, HPMC / Wet gelatin and other similar products. We offer completely customized systems adhering to cGMP and ASME BPE guidelines for aseptic manufacturing.
We offer a full range of process vessels and their automation - comprising optional SCADA package - as well as all associated peripherals including suction pumps, CIP/SIP systems, and the stand mounted stirrer assembly.
Benefits
- 1Gelatin melting mixer to get bubble free gelatin solution
- 2Color addition system with interchangeable vessel design
- 3Multipurpose holding vessels
- 4Medicament mixer with homogenizer
- 5Heat traced transfer pipeline for in feed encapsulation line
- 6CIP & SIP equipped
- 7Fully automated system with PLC HMI, can also be incorporated with SCADA with 21 CFR Part 11
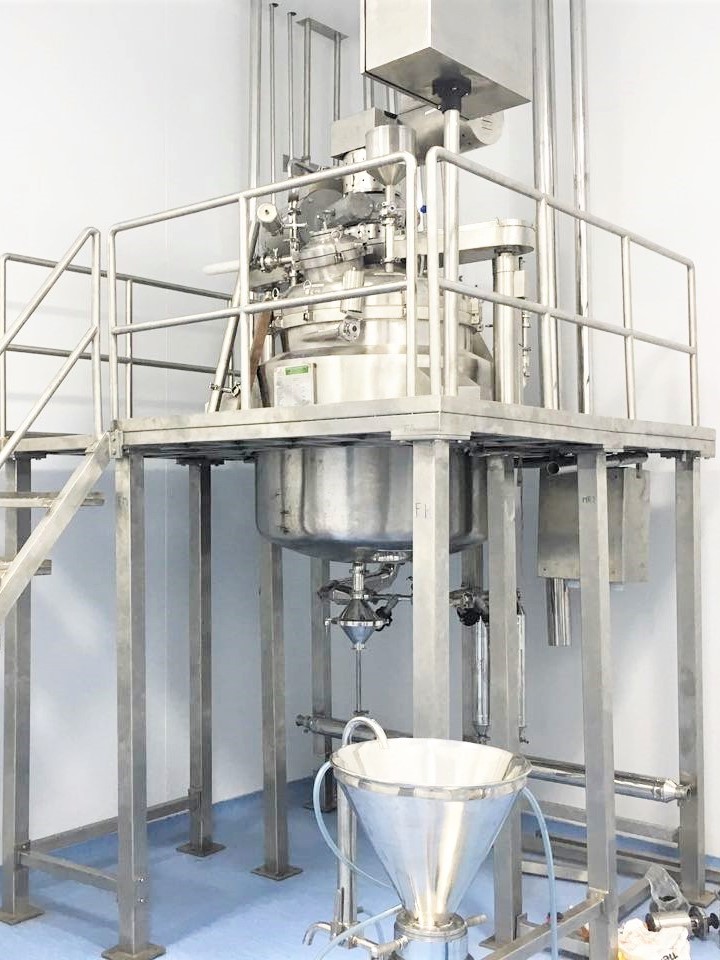
We offer the following customizations according to client specific needs,
- Jacketed gelatin melting tank
- Jacketed medicine mixing vessel
- Gelatin Holding vessel
- Medicament Holding vessel
- Stand mounted stirrer / Homogenizer
- Color mixer
- Vacuum pump
- Transfer pump
- Control panel
- Interconnecting pipeline
- Working platform
- Automatic Temperature Control with PID
- Load Cells
- SCADA system architecture
A standard gelatin capsule manufacturing takes place in two different vessels – A gelatin melting tank and a medicine mixer. Other components may include an emulsifier/homogenizer, a vacuum pump, Transfer pump, storage and buffer vessels and a CIP module. All our vessels are made of SS316L grade material and fabricated as per cGMP guidelines. The plant can be completely automated with pneumatically operated valves for aseptic manufacturing.
Gelatin melting vessel
Mixing and melting of gelatin, purified water & glycerine is carried out in the gelatin melting vessel. Each product is sucked into the vessel at vacuum pressure for minimum contamination. The vessel is jacketed for heating & cooling of the solution in the vessel. For uniform mixing, an anchor type stirrer is utilized along with Teflon scrapers. A high shear mixer or emulsifier is used to reduce the particle size of gelatin powder to less than 5 microns. The contents can also be recirculated back into the vessel via a transfer pump based on the product viscosity. Deaeration of the solution is also done during heating. After obtaining the satisfied composition, the contents of the vessel are transferred to a gelatin holding vessel.
Medicine mixing vessel
The contents of the medicine in the final product is prepared in the medicine mixer. The ingredients are sucked into the vessel at vacuum pressure for minimum contamination. The vessel is jacketed for heating & cooling of the solution in the vessel. For uniform mixing, an anchor type stirrer is utilized along with Teflon scrapers. After obtaining the satisfied composition, the contents of the vessel are transferred to a medicine holding vessel via a transfer pump.
The operations of various pumps, pneumatically operated valves (in case of automated operation) and mixers is carried out through the main control panel. The panel is made out of SS304 grade material and consists of various safety lock systems like the Emergency stop and Mains supply indicators for safe work and extended component life. The vessels are connected to each other via interconnecting pipelines manufactured as per cGMP norms and connected with sealed tri clamp connection.
Features of our system:
- Uniform ingredient dispersion
- No wall caking
- Entire plant operation by one operator and one helper
- Efficient heat transfer in the vessels
- Particle size reduction less than 5 microns
- Reduced batch processing time
- Reduced change over time
- Consistent product composition across different batches
- All contact parts made of SS316L and non-contact parts made of SS304 grade material
- Food grade silicone gaskets
- Vessel design as per ASME guidelines
- Torispherical, Hemispherical and Conical dish top customization availability
- Hydraulic lid lifting arrangement for occasional cleaning
- Static & Dynamic spray ball availability
- VFD for motor rpm controls
- Double cartridge mechanical seal along with cooling arrangement for Homogenizer shaft