

Factors that affect the CIP performance
Vessel clean-in-place systems (CIP), first introduced in the 1950s, were a tremendous improvement in processing operations, eliminating the need to manually disassemble vessel systems for cleaning, and leading to significant gains in product safety and production efficiency.
CIP systems deploy spray balls mounted through the top head of the vessel and connected to inlet lines. The spray balls use pressurized water and cleaning solutions to wash residual product off the inside top and inner vessel walls down through the discharge outlet, thereby cleaning and sterilizing the vessel for the next batch.
Spray balls can cover a wide area inside a vessel, with the most common spray ball options providing for 180-, 270- or 360-degree vessel coverage. During the CIP process, the spray ball’s water pattern must reach the many fittings which often extend through the top head of the vessel that hold various probes, sampling ports and other processing and control fixtures extending into the vessel.
To optimize your vessel’s CIP performance, cleanability and drainability must be considered from the beginning stages of your design. Here are some key guidelines for designing CIP capability into your processing vessel:
- Use sufficient nozzle sizes for CIP sprayball fixtures: A sprayball inlet nozzle size of at least 1.5" ensures sufficient flow of water and solution for cleaning. Inlet sizes which are too small may not carry enough volume and flow pressure to reach certain areas farther away from the sprayball on the inside of the vessel
- Minimize the number of sprayballs used in the vessel: While adding more spray ball nozzles may seem like the easiest design approach for increased vessel cleaning performance, additional sprayballs require a higher flow volume of specialized water and cleaning solutions, resulting in higher processing costs. You may be better off modifying a smaller number of sprayballs to optimize their individual performance
- Determine if special vessel features require additional or customized sprayballs for better coverage: In certain instances, it may be necessary to place an additional or customized sprayball to reach special vessel features, such as a manway port in the vessel's top head. In some vessel designs, sprayballs attached to each end of a specialized "T" fitting can also be used to extend coverage.
- Position interior nozzles for ready sprayball access: All interior nozzles used for monitoring, access, sampling or control features should be grouped together and positioned within the vessel so they are easily reached by the "cone" created by the sprayball water jets. Also, it is important to minimize the length and profile of all nozzles which extend into the vessel. The longer the nozzle, the harder it is to clean.
- Modify sprayball water jets to reach targeted areas: Additional holes can be drilled in sprayballs to provide extra water jet openings to reach specific areas inside the vessel. Once drilled, each sprayball can then be custom pinned to its specific inlet nozzle and specially marked ("etched and pinned"), to exactly position the sprayball for repeatable cleaning results.
- Consider exterior piping requirements when designing sprayball placement: In some cases, the configuration of exterior process and inlet pipes on the vessel's exterior may require the sprayball be positioned in a certain area inside the vessel.
- Specify vessel drainage rates higher than CIP flow rates: The vessel's drain output capacity should always be higher than its CIP inlet capacity. This will prevent pooling in the bottom of the tank during draining, which can deposit unwanted rinse water or cleaning solution at the bottom of the vessel during the cleaning cycle
- Avoid "dead-legging" in nozzles, drains, and fixture placement: "Dead-legging," caused by hidden spaces and gaps within outlet drains, fittings and other vessel fixtures, puts these areas out of reach of sprayball coverage. Eliminating excess piping lengths and other gaps in these interior vessel fixtures removes areas where unwanted product can collect during the vessel cleaning process.
- Specify high finish grades for vessel interiors: Your vessel’s finish plays a major role in assuring thorough cleaning and draining during the CIP process. A surface finish of 20 RA or better, using electro polishing, provides the lowest surface tension and allows water and cleaning solution to drain quickly from the vessel.
Incorporating these guidelines into the design of your next processing vessel will strike the best balance between CIP performance, production rates and processing costs, and will help your company meet stringent processing sanitation and product safety requirements.
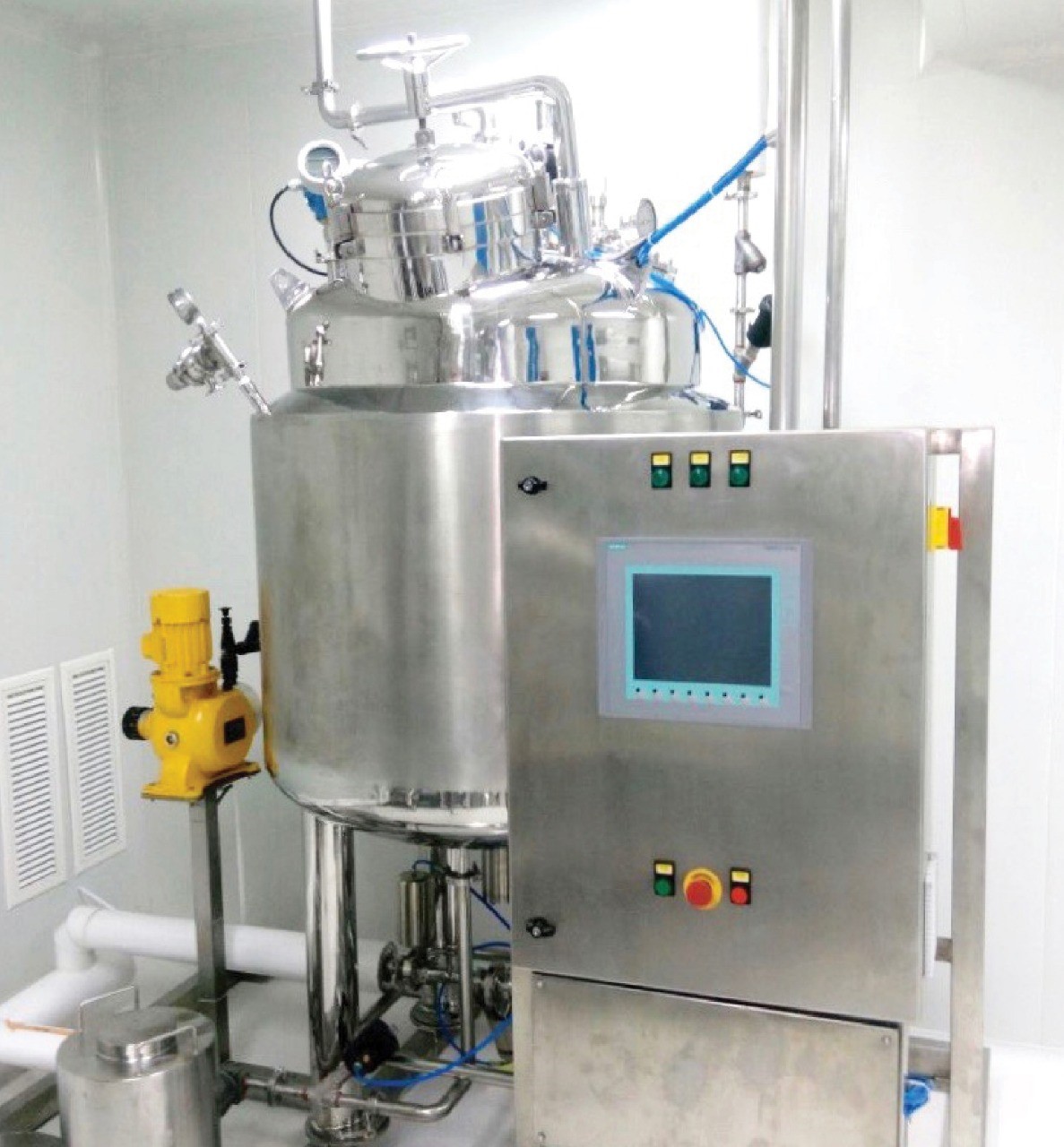
For more Connect to us.