
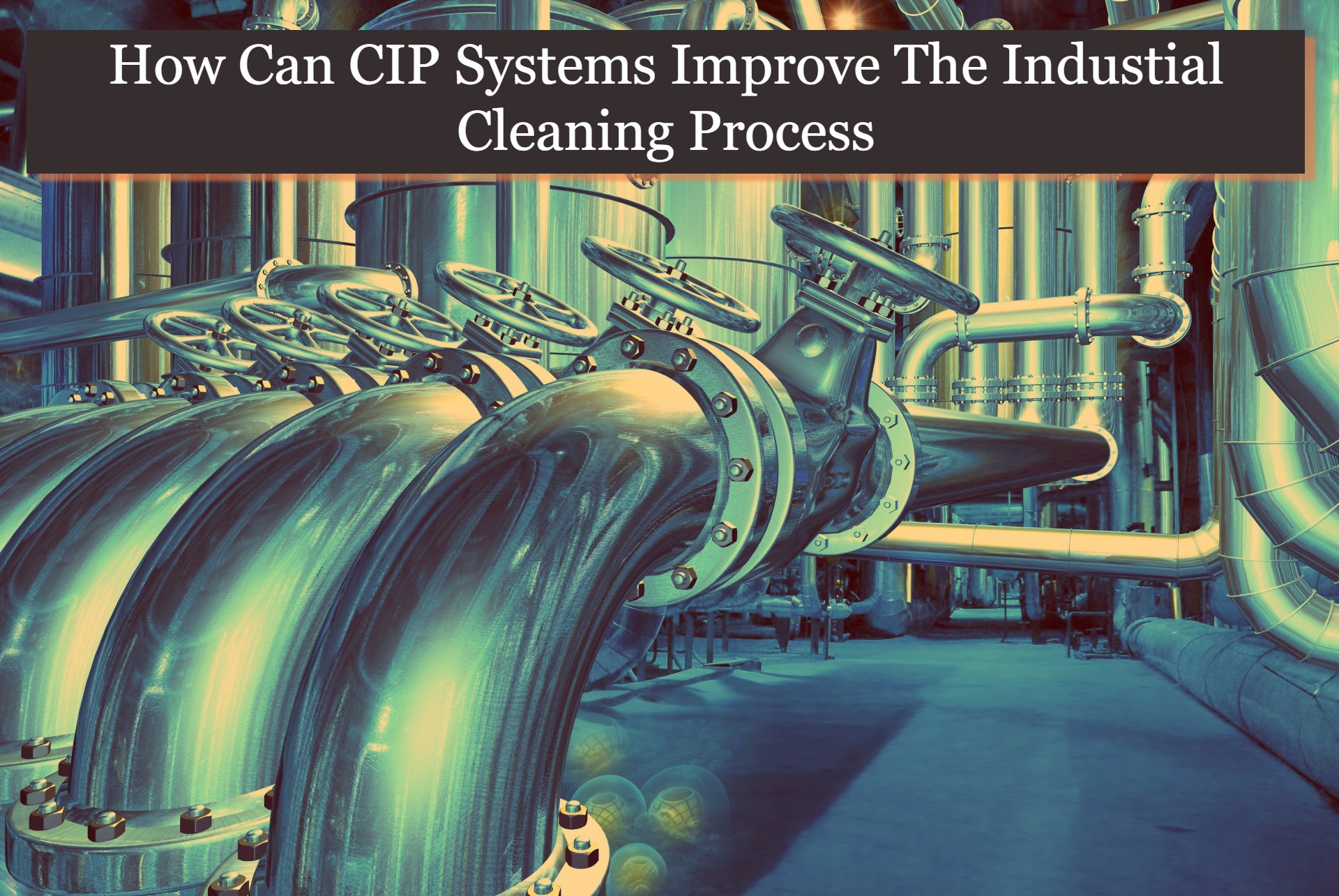
How can CIP Systems Improve the Industrial Cleaning Process
One of the key reasons behind the implementation of CIP systems is hygiene. Hygiene plays a very significant role in the manufacturing process and is one of the most important factors in the manufacturing industry, especially in like Pharma, healthcare, biotechnology and cosmetics industries. To maintain hygiene, monitoring has to be done and precautions have to be taken to check whether the product and working personal are free of contamination or not. If the product is free of contamination, then the product is considered to be of highest quality. Different types of machinery and machine parts are associated with the production machinery such as vessels and pipes. These parts come in contact with the various ingredients during the time of manufacturing. While cleaning the product lines, it has to be checked whether these parts are also cleaned or not to ensure good product quality. Hygiene should be emphasized in various sectors of the industry such as production facilities, equipment, storage systems and many more.
CIP systems is an automated cleaning method in which different parts associated with the product line such as vessels, pipes and fittings are cleaned without any major disassembly. CIP system is an efficient method to ensure hygiene. It plays a vital role in cleaning of product lines irrespective of the industrial sectors such as facility, drug manufacturing plant, laboratory and other pharma operations. Through CIP procedure, effective cleaning and sterilization process of equipment is carried out on a regular basis to ensure minimum contamination and product quality. The product quality is supervised and it is checked whether the product is suitable for consumption or not.
A large number of products are manufactured in the production facilities and sometimes the composition of the product is purposely varied to change the dosage. This process involves the use of APIs and so a special procedure is applied to prevent product carryover. CIP systems are one of the best methods when it comes to the prevention of cross-contamination.
CIP is used to clean various parts of vessels including pipes, joints, contact surfaces, piping, pumps, filtrations skids without dismantling them. This process saves the cleaning cycle time and ensures reliability and consistency of the entire process.
There are various factors associated with an effective cleaning CIP cycle such as cleaning time, , coverage area of the surface, chemical concentration and temperature. Generally, more the recirculation less is cleaning time, the better is the end result. Proper sizing of pumps, paths and spray devices and other components play a vital role in the cleaning process. Cleaning validation can help to optimize the cycle timing during the qualifying stage. The next important factor is action. A deep understanding of the type of residue is necessary for the execution of the CIP process. The more the viscosity of the product, the more is the cleaning recommended. Other factors such as the selection of spray balls, increase in velocity of flow, pressure should be monitored to obtain a smooth flow and prevent turbulence. Another important factor is the coverage area of the surface. Spray devices such as spray nozzles, spray balls and lances distribute, wash and rinse the inner surfaces of the product. Spray devices are available in various designs such as static or dynamic. Chemical concentration also plays a vital role in the CIP procedure. Chemicals and detergents help to reduce the cycle time of the cleaning process and improve the efficiency of cleaning. The detergents should be compatible with the product and should comply with the cleaning guidelines. The concentration of the chemicals and detergents have to be validated. The temperature for CIP systems differs and depends on the cleaning cycles and products. The primary rinsing process can be performed at ambient temperatures. The temperature is optimized to ensure that there Is minimal energy loss due to overheating, nature of detergent and recess of pumps. The recirculation of CIP solution reduces overall cycle time and also gives better results in terms of clean ability of inner surface.
Let us discuss some of the advantages of a CIP system:
The modern CIP systems are provided with automated systems to ensure effective cleaning. These automated systems comprise devices such as temperature and conductivity sensors & PH Sensors. These CIP structures have customizable skids such as single tank systems and multiple tank systems. These CIP structures have CIP skids with alkali and acid dosing provisions.